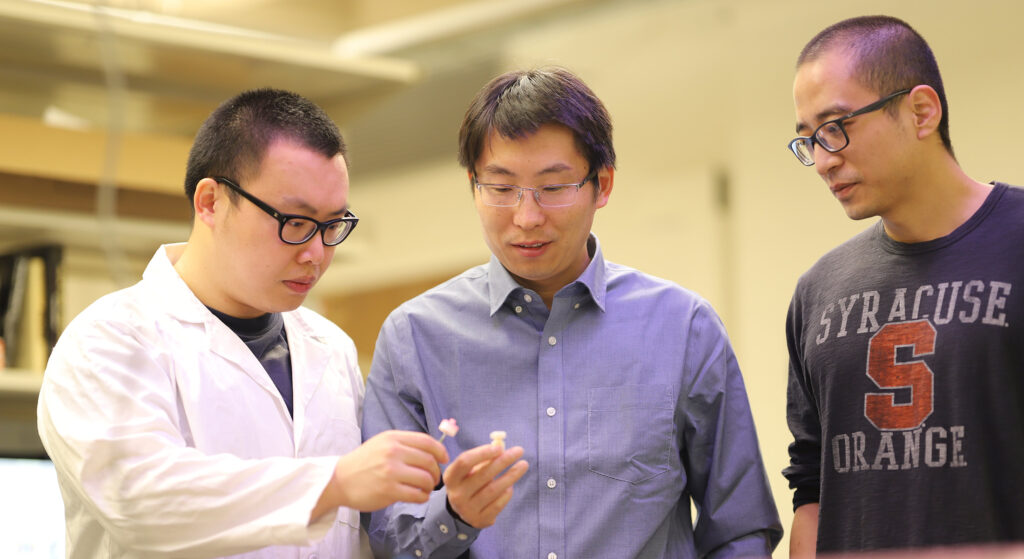
Assembling electronic devices requires precision and the ability to place key components in tight spaces. Manufacturing systems need the ability to grip a component and then release it in the right spot. To make it even more challenging – the grippers need to be tiny and able to grip and release items that are measured in microns.
Mechanical and aerospace engineering Professor Wanliang Shan started considering the problem in 2016 while he was at the University of Nevada – Reno and was awarded a National Science Foundation (NSF) Materials, Engineering and Processing grant to explore the concept.
“I wanted to see if we could use smart materials to design and fabricate a soft gripper of composite structure with tunable adhesion. By running current through the smart material component, we could change it from rigid to soft and release objects due to reduced adhesion of the gripper,” said Shan.
The proof of concept Shan’s research team designed was successful in realizing a ~10 times dry adhesion change within a matter of seconds. Their work was published in the Advanced Materials Interfaces journal in 2018 and Shan was granted a patent in the spring of 2022.
“One of the advantages of this technology is that it could save energy compared to traditional suction cups,” said Shan. “When you pick things up the gripper is in the high adhesion state, only when you release do you use current to activate it.”
Shan has completed an NSF Innovation Corps project to conduct interviews with over 100 potential customers for the compliant manipulation technology and concluded that there is tangible industry demand for it. He has most recently received an NSF Partnership for Innovation (PFI) grant to see whether it is reasonable to set up a company and commercialize it.
“This is a new approach for how to manipulate objects,” said Shan. “Through the PFI project we will see if potential customers like our prototype. If it is successful, what will it focus on?”
As part of the NSF PFI grant, Shan and his research team are partnering with Cobham Advanced Electronic Solutions for market testing and customization options.
“I’m very thankful for the support from the NSF,” said Shan. “They fund essential research, customer discovery, prototype development and partnership building.”
Shan and his team are also developing a second approach to a soft gripper that uses pneumatics to tune adhesion. That research has received funding from the NSF National Robotics Initiative. Their most recent progress along this direction was published in the high-impact journal, Advanced Functional Materials. The research shows soft grippers with over 100 times dry adhesion change within one second when triggered by low pressure (~10 kPa) and thus low power consumption has been reported. Shan and his post-doctoral researcher Dr. Guangchao Wan filed for another patent on this approach in September 2022.
“We don’t use suction which is typically ~50 kPa, we use low pressure to affect adhesion to the object being gripped.”
Shan’s lab is pursuing both gripper approaches and he sees potential and challenges for both to succeed in different applications.
“They are different methods with different activation modes but parallel approaches,” said Shan. “Depending on the environment, we could see which one is better. Both approaches have a lot of potential to solve tangible challenges in industry. Smart materials that satisfy the needs of this technology are yet to be engineered; pneumatics is readily available in industry but it might present a more challenging task for minimization than the smart materials approach. Currently we are focusing on improving the performance of both approaches through the PFI project and other parallel efforts.”