The mechanical engineering senior capstone design course is a rigorous two-semester engineering experience intended to simulate developing a product in an industry setting. These industry-sponsored projects are designed to support the development of teamwork, critical thinking, problem solving abilities, communication skills and other key areas of expertise that prepare students for their careers. The industry partnerships provide students with valuable real world experience and networking opportunities, and the sponsoring companies receive innovative solutions to problems and the opportunity to recruit elite, young talent.
The course is co-instructed by Kenneth and Mary Ann Shaw Professor of Practice in Entrepreneurial Leadership Alexander Deyhim, and Mechanical and Aerospace Engineering Professors Mehmet Sarimurat and Ed Bogucz. Professor Deyhim describes the course as an immersive experience that pushes students to achieve excellence.
“The progress of each project is meticulously monitored through a gated review process. This process entails regular feedback and evaluation from multiple stakeholders, including the client, faculty members, fellow students, and a review panel,” says Professor Deyhim. “By engaging in this iterative review system, students receive valuable insights and recommendations at various stages of their project, facilitating continuous improvement and aligning their efforts with the client’s expectations. This year, seven teams completed capstone projects; the final presentations were excellent, and every single team impressed our esteemed panel of industry judges.”
Here are the 2022-2023 mechanical engineering senior design capstone projects:
Additively Manufactured Cold Plate
Sponsor: Lockheed Martin
Working with Lockheed Martin, the team designed, tested and determined the best way to produce an additively manufactured (3D printed) cold plate to be used in various applications for the company’s numerous radar electronics. This is a critical design because Lockheed Martin’s products can reach temperatures up to KW/cm2. The team evaluated multiple designs with complex geometric flow paths and determined appropriate material for manufacturing the cold plate while considering cost and functionality.
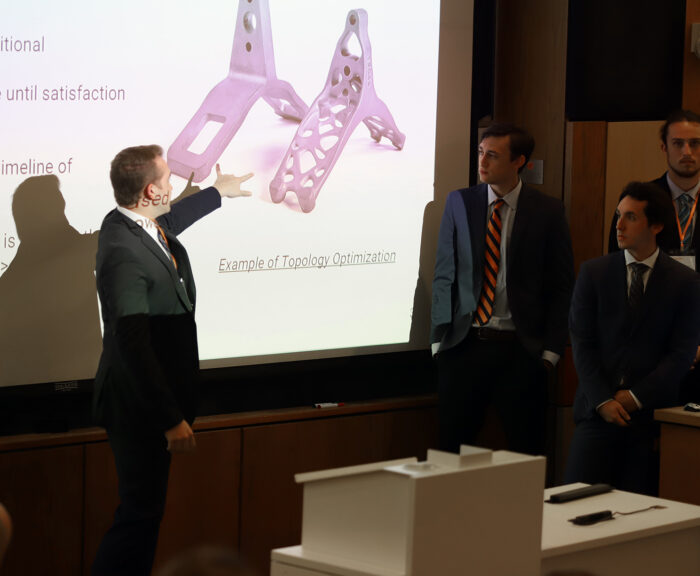
Automated Inspection of Jet Engine Components
Sponsor: GE Aviation
The team advanced the development of a solution allowing the inspection of turbine discs using cameras and artificial intelligence to determine if there are any small cracks or defects that could damage the engine. The goal of this project was to design a system to remove human error and increase efficiency of the inspection process. The team assisted GE in developing an automated white light digital system for the part inspection with a focus on pass-through features.
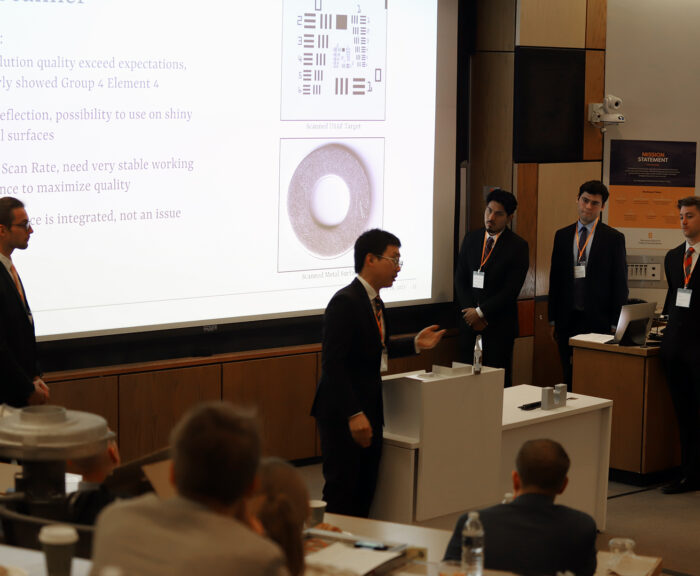
Dairy Cover and Conveyor Belt Cleaners Redesign
Sponsor: Berry Global
The team was tasked with helping Berry Global, an international plastic packaging company, to increase the efficiency of their injection molding process. The team provided a design and prototype for a portable way to clean the cover from the ground without needing to stop production. The proposed design is an automated device that sits on the framework of the dairy covers and will sweep debris and particles into dustbins located on the two sides on the dairy cover.
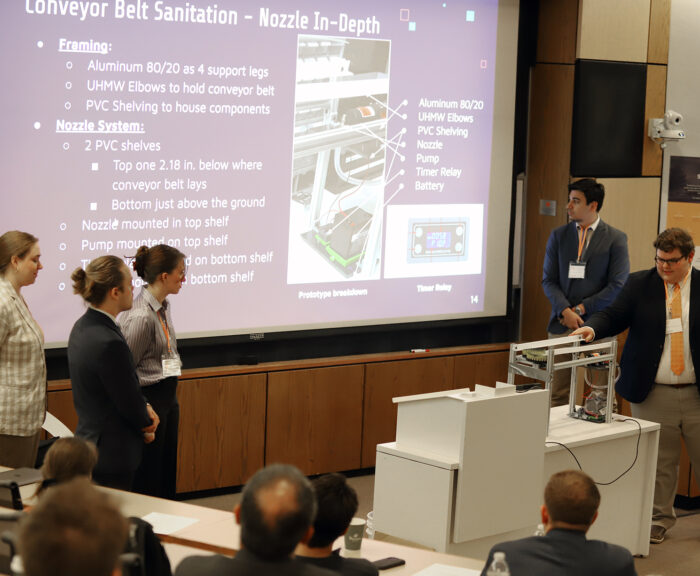
Compact High Efficiency Air Handling Unit
Sponsor: Upstate Parts & Supply Inc.
Centrifugal fans have been at the forefront of cleanroom technology and have been the industry standard for a long time. Mechanical and Aerospace Professor Mehmet Sarimurat and Former Mechanical and Aerospace Engineering Professor Thong Dang designed a new axial fan to be utilized in a microchip manufacturing plant (Class 1000) which uses less energy. The team’s role was to first design an FFU (fan filter unit) that can house the fan while being compatible with a high efficiency particle arresting (HEPA) filter. Once the designed FFU and fixture system were in place, the team conducted performance testing of the fan with attention being paid to how the designed system works with the fan and if the performance is superior to a traditional centrifugal one.
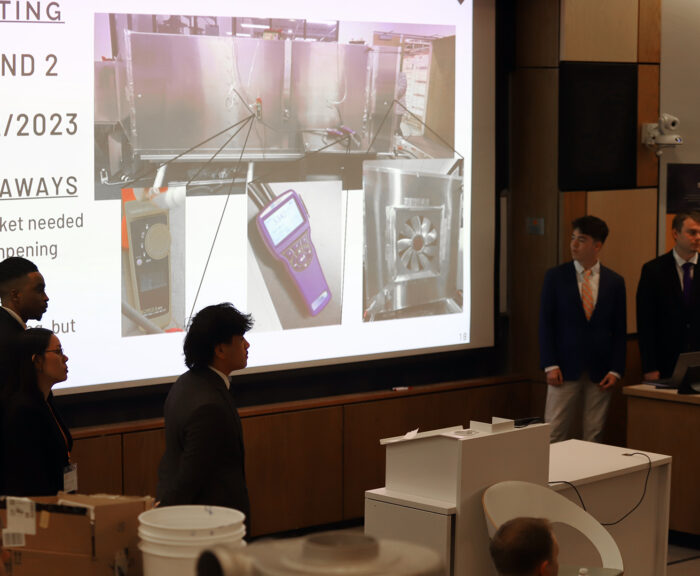
Occupancy Based Smart Vent
Sponsor: WellBuilding Control
WellBuilding Control is a company started by Mechanical and Aerospace Engineering Professor Dr. Bing Dong, whose research focuses on heating, ventilation and air conditioning (HVAC) systems. The team was brought in to focus on developing an occupancy control HVAC system that will reduce energy consumption in heating and cooling buildings. This system will reduce carbon emissions and save money for consumers. The team concluded that an automated air register vent would be the most effective method of achieving the goal. The team then created a design and prototype of a control vent that will open and close automatically when a room becomes occupied or unoccupied to control the air flow to that room. The vent will also control indoor air quality using a CO2 sensor that will turn on a fan that will blow air and reduce the CO2 levels.
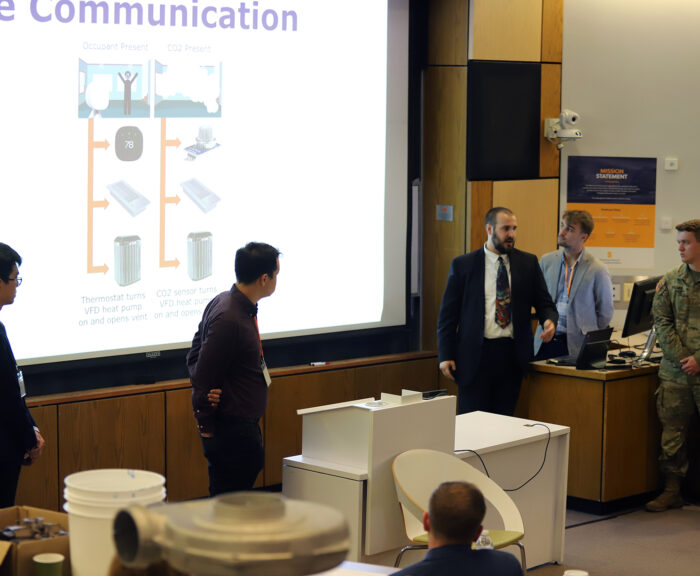
Desiccant Hopper Redesign
Sponsor: Cryomech
The team was brought in to help Cryomech, a manufacturer of cryogenic cooling applications that use helium gas as the working fluid in a helium compressor, to design an improved hopper system. Helium compressor packages made by Cryomech use desiccant adsorbers to “clean” helium as it is cooled to temperatures as low as 4K. Currently, the molecular sieve and granular activated charcoal used in the adsorbers is being contaminated from atmospheric exposure. The team designed and created a prototype of a hopper system that will keep the desiccants clean and reduce production time.

Integrated Sustainable Building Design Competition
Sponsor: ASHRAE
The team entered the 2023 Integrated Sustainable Building Design Competition, specifically the HVAC Design Calculations competition. The project’s objective was to fully design an HVAC system for a laboratory facility located in Cairo, Egypt. The team submitted a 35-page technical report including all the work and calculations, along with analysis explaining the logic. For this competition, the team was required to adhere to the most up to date American Society of Heating, Refrigeration and Air-Conditioning Engineers (ASHRAE) standards. Representatives from Carrier Corporation also mentored the team, assisting them with the ins and outs of learning their Hourly Analysis Program (HAP) software to get the load calculations.
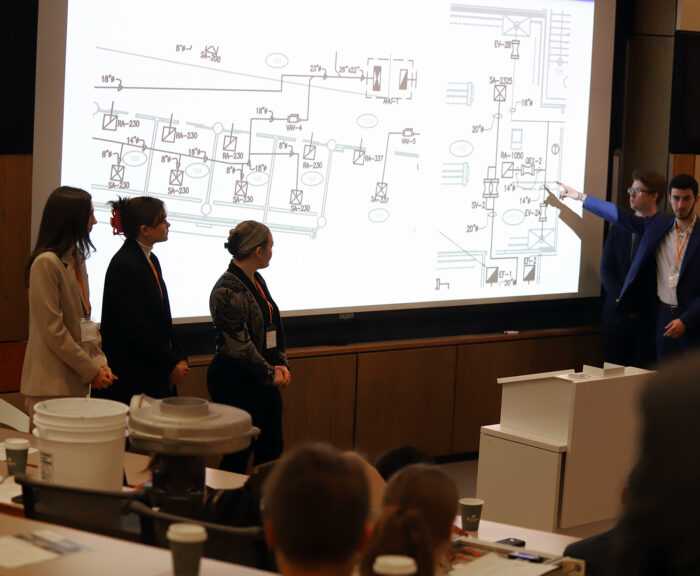